In the poultry industry, margins are razor-thin, and every penny spent needs to pull its weight. For too long, poultry companies have leaned on diagnostics and contract labs as a crutch, ticking compliance boxes and relying on gut instinct to make important decisions. But outdated tools and guesswork does not make for a reliable strategy, and more tests aren’t the answer.
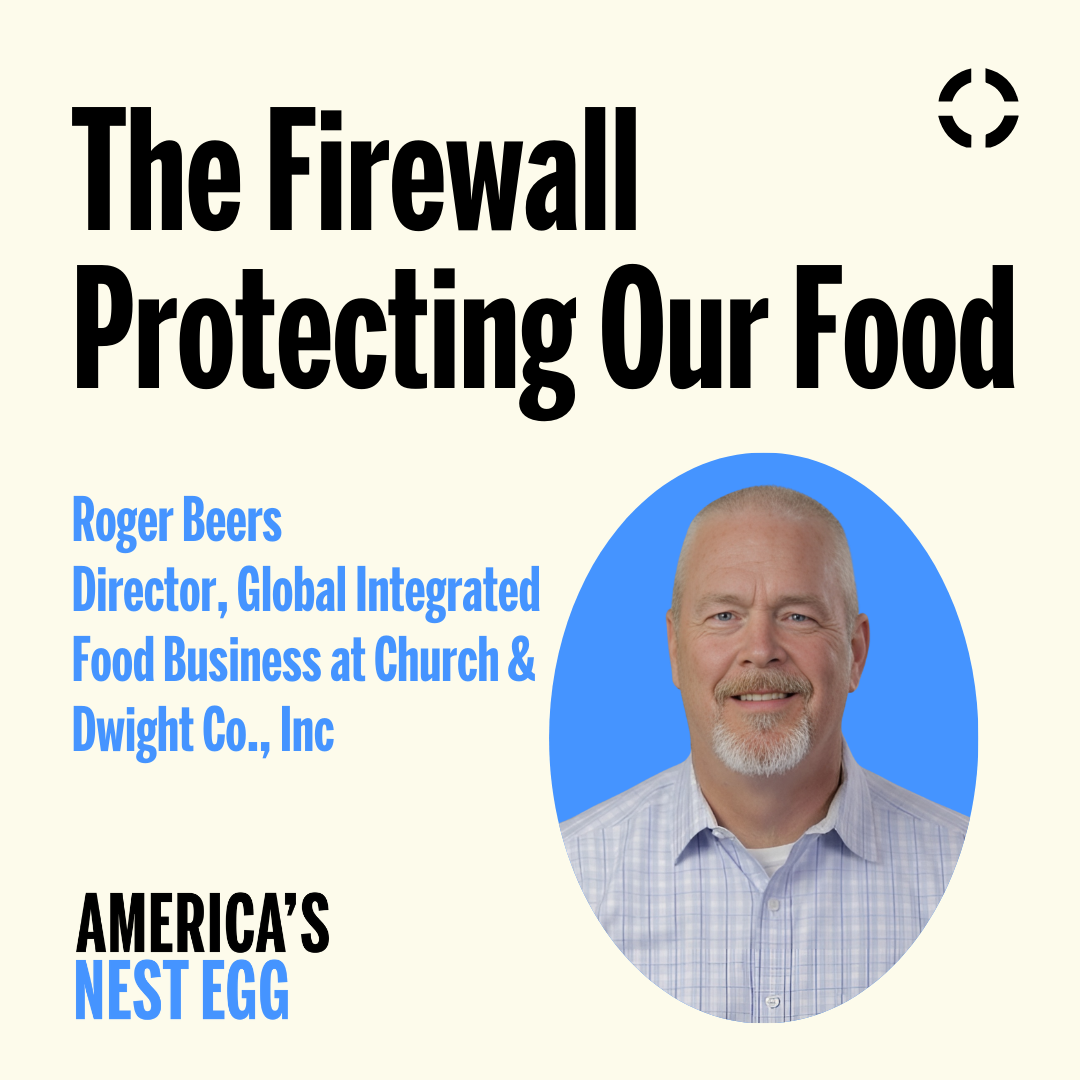
Publication
Fortifying Our Food Defense System with Roger Beers
On a recent episode of America’s Nest Egg, host and Ancera CEO Arjun Ganesan spoke with Roger Beers, Director of Global Integrated Food Business at Church & Dwight Co., Inc.
Roger Beers is a leader in animal science and food production markets whose three decades of experience include time spent at Packers Sanitation Services, A&L Laboratories, and EcoLab. He’s a veteran of the United States Army and an indispensable asset to America’s food defense system.
During the podcast conversation, Beers discussed topics including food production silos, a firewall protecting our food, and the “third shift” in sanitation.
Decades of Food Defense
With over 30 years of experience across the food chain, Beers brings a unique perspective to America’s food industry. He credits his time in the United States Army as an integral part in the way he approaches food quality and food safety operations. During one specific intelligence-gathering mission, his team was stationed in a strategic location to identify enemy activity, but there was none.
“I had encrypted a message back saying, ‘Hey, pull us out and put us somewhere where we can make an impact,’ and the message I got back was basically, ‘We need to know where they're at just as much as we need to know where they're not,’ speaking of the enemy. And I look at that lesson that I learned 35 years ago and it's even more true today as we look at the food safety culture and developing a strong food defense system. We need to know where the pathogens are just as much as we need to know where they're not.”
After his time in the military, Beers attended the University of Wisconsin River Falls where he studied agricultural science, food science, and business management. His degree and experience landed him a job at Ecolab, a Fortune 500 company, managing and leading their global engineering food and beverage business.
“For the last 35 years I've been in various jobs across the food chain where I've had the opportunity to not only work in one segment, like the processing segment, but look at that impact all the way from the beginning out on the farm, and I think it gives me a unique perspective because I'm not in a silo,” Beers said.
Baking Soda and Animal Health
Arm & Hammer is a brand of its parent company, Church & Dwight, a publicly traded company on the New York Stock Exchange. Beers has been a Director at Church & Dwight for nearly 4 years now. The consumer products company has a 150-year legacy largely built on its Arm & Hammer baking soda, which has a variety of uses including toothpaste, laundry detergent, and odor control. One lesser-known use of baking soda, or sodium bicarbonate, is in animal dietary rations.
In 1956, Arm & Hammer noticed that a pharmacy in Indiana was buying massive quantities of baking soda and decided to further investigate the use case. They found that the pharmacy was using the product in dietary rations for dairy cows to act as a buffer, or an acid reduction. That’s when Arm & Hammer realized they had a new, untapped business market in animal nutrition.
“From the mid 1950s forward, once they realized they were a major player in the animal nutrition business, they started to expand their portfolio and they brought products to market that focused on animal nutrition, animal performance, and building resiliency in animals in the production environment.”
Fast forward to today, Church & Dwight continues to play a major role in animal nutrition throughout the food supply chain, addressing antimicrobial application, reducing pathogen loads, and building resilience in the food safety sector.
“Today, we're the only company that I'm aware of that has the ability to bring microbial and antimicrobial solutions across that entire food processing chain,” Beers said.
Overcoming Production Silos
One major challenge in food production is breaking down production silos. It’s not a simple answer, but Beers said that one focus has to be on recognizing commonality.
“Commonality helps break down those silos. And by that I mean if two or three people, or two or 300 people, are all working together and they understand and share a common vision for what their work is, even though they may play different roles in the chain, if they have a common vision, if they have a common mission, which is what they get out of bed each and every day to go and try and achieve, they share common values clear objectives and they understand the metrics around measuring performance against those objectives, you can start to break down those silos.”
Throughout the food production chains, silos are created by different incentives and rewards from one link in the chain compared to another. One example provided by Beers, a farm manager is compensated, rewarded, or recognized for something completely different than a plant manager or an executive group that oversees the entire integrated process. Seeing commonalities in these chains rather than the differences is key to overcoming production silos.
A “Firewall” Protecting Our Food
America needs to create an “Iron Dome” for the food safety system. There are breaches every day throughout the world that threaten the food supply, and according to Beers, we are not as focused on tracking and stopping those breaches as we should be. Rather, our system is more reactive than proactive.
“We use a lot of chemistries as interventions without maybe always knowing exactly what we're trying to do. So we use broad spectrum antimicrobials. Part of what that's led to is it's definitely had a positive impact, but for every action there's an equal and opposite reaction.”
The opposite reaction has been a broad use of acid-based antimicrobials, which pathogens can build a tolerance to. According to Beers, a new “firewall” protecting our food system involves use a multi- hurdle, multi-intervention approach that not only continues to use some of those current acids that are that are effective, but also offsetting that with other technologies that are a higher on the pH scale that attack it from a different way.
“I'd argue that we haven't gotten to the point where we truly understand the levels we need to use in order to be effective and also how we use other technologies with different pH structure, etc., that will better optimize the overall effectiveness of that food defense system.”
Understanding the Threat of Microplastics
Concerning the threat of microplastics, Beers said it goes back to understanding the enemy. It’s important to identify the threat, the potential damage it can cause, and where they are being introduced into the system in order to better manage it.
“The Graduate I think was the movie where in 1965, the future was plastics. Well that's reality today. What food doesn't come packaged in some form of plastic? I just saw an article last week I believe in the news about a beverage company being sued because of microplastics in their water bottles. Until we know that's a threat, how do we call it an enemy? And then if we do call it a threat, we need to think through how we mitigate that threat, how we eliminate that threat.”
Beers continued that even though we identify microplastics as a potential threat, we have to come together as regulatory organizations, manufacturing organizations, and the industry to bring common “vision, mission, values, objectives, and metrics” around the problem in order to solve it effectively.
The “Third Shift” in Sanitation
When Beers worked at Packers Sanitation Services as the vice president of sales and marketing, one area he focused on was getting the a better understanding picture around what role the company played in the industry.
In sanitation, the ‘third shift’ in a production schedule is often looked at as the last stage of the day and therefore the lowest priority when it comes to sanitation. Beers worked to redefine this shift as the most important.
“In my mind, third shift was more important in an order of priority than first shift because all of the burden fell on that team in that shift zero in order. That's what I changed it to was ‘shift zero.’ It's the beginning and it's the end. If you don't do your job, that plant doesn't go into production and we've got some challenges and if you do your job, then the first shift can come in.”
This change had an impact on career advancements as well. When employees entered the company, rather than seeing the third shift as the lowest on the totem pole, they saw the shift as the beginning and then end of the production line.
America’s Nest Egg
The America’s Nest Egg podcast hosts conversations on the poultry industry, biotech, and more. Listen to the full episode with Roger Beers.
Subscribe to America’s Nest Egg and join the conversation.