In the poultry industry, margins are razor-thin, and every penny spent needs to pull its weight. For too long, poultry companies have leaned on diagnostics and contract labs as a crutch, ticking compliance boxes and relying on gut instinct to make important decisions. But outdated tools and guesswork does not make for a reliable strategy, and more tests aren’t the answer.
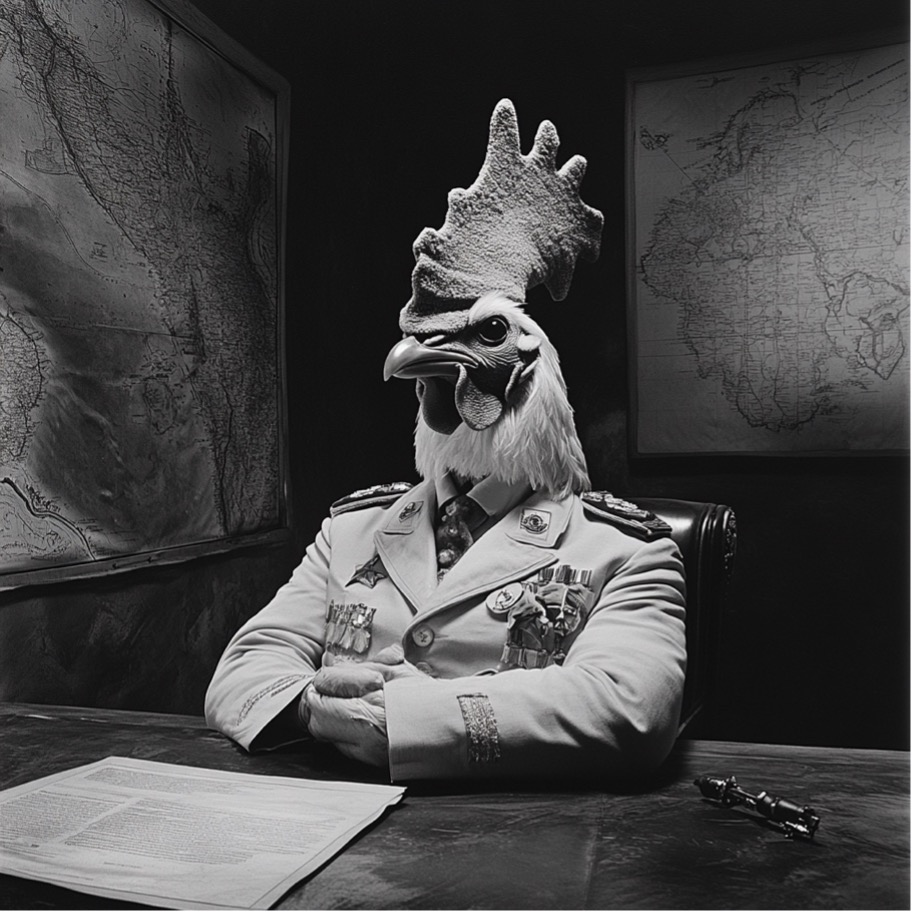
Publication
Why Blanket Downtime Schedules are a “Profit Killer” in Small Bird Operations
Small bird complex targeting $4.31 Million in new profits by switching from blanket schedules to precision-downtimes between flocks.
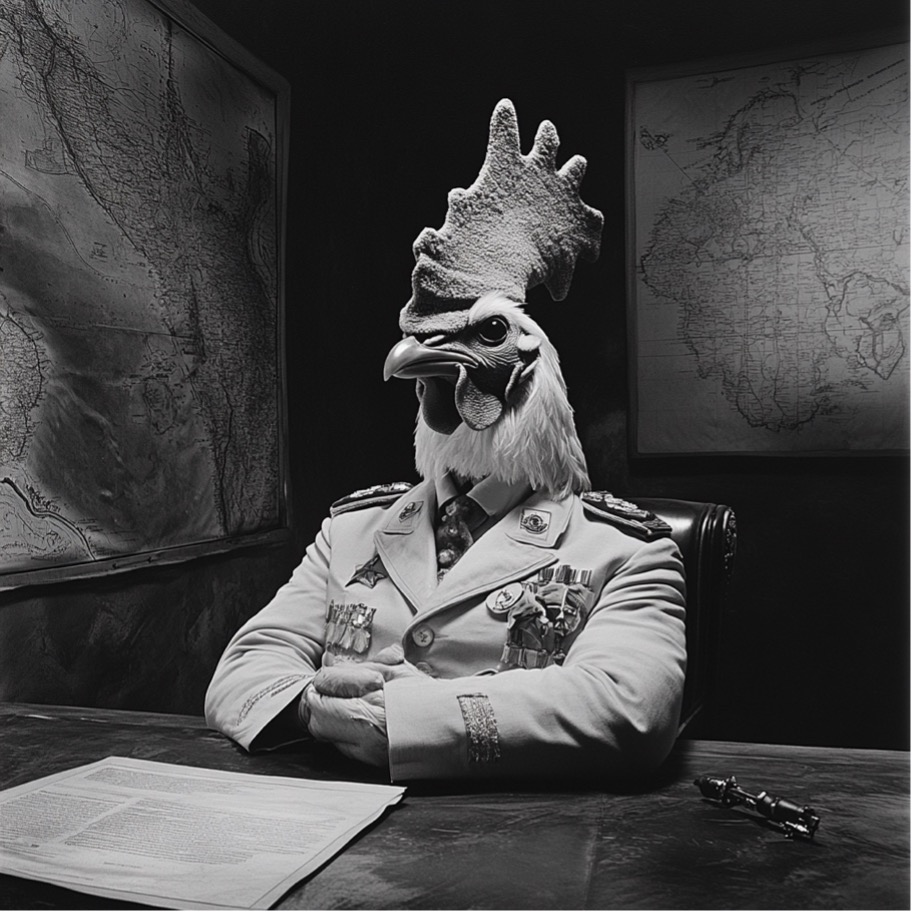
In the poultry industry, integrators will win when they know when to intervene and when not to intervene. In war, it would be folly to approach every battlefield with the same troop formation and tactics.
This is unfortunately the status quo in live operations, where broiler managers and service techs fights microbes across hundreds of houses – ignoring the varying levels of productivity and risk. Downtime between flocks take a blanket “one-size-fits-all” approach –applying the same number of days for cleanout or treatments based on routine schedules.
Fixed downtime is a safe and uniform practice that caters to the average farm but guaranteed to lose money on houses that don’t need a full reset before the next flock. The challenge is knowing which farms are ready for the next grow-out, which need the standard downtime, and which need additional treatment to mitigate bacterial and pathogen risk.
When every unnecessary day of downtime costs $1,500 and a complex can process 1,000 flocks a year –the lost dollars and cents rapidly eat into poultry margins. Then those losses extend to second order effects such as increased mortality and loss in feed efficiency.
Ancera is pioneering anew data-driven modern approach. The initial data show nearly one third of flocks are ready for expedited treatment and can safely shave off 1,000 downtime days per year.
Precision Downtime: A Case Study in Profitability
Take a small bird complex that recently adopted Ancera’s Precision Downtime approach. By replacing the traditional blanket approach with a data-driven strategy, this complex is on track to unlock millions in new profits.
Here’s how it works:
→ Real-Time Data Collection: Ancera’s next-gen microbial detection technology measures conditions in each poultry house. Analytics and data science algorithms analyze a variety of microbial information that impact broiler performance to develop baseline trends and predict changes in house conditions.
→ Tailored Downtime Recommendations: Based on the data, the platform generates four downtime options for each farm, ranging from shaving off three days where it is safe to do so, to an extended downtime where problematic conditions still linger.
→ Field Tech Integration: Broiler managers can send targeted work orders to field techs, ensuring each farm gets exactly what it needs—no more, no less. Let’s say a variety of microbial information on microbial composition, pathogen loads, and factors affecting bird productivity.
→ Full Visibility and Accountability: Everyone gets visibility and the ability to act on real-time data – from the VP of Live Production to broiler managers to service techs – ensuring everyone works towards a common goal.
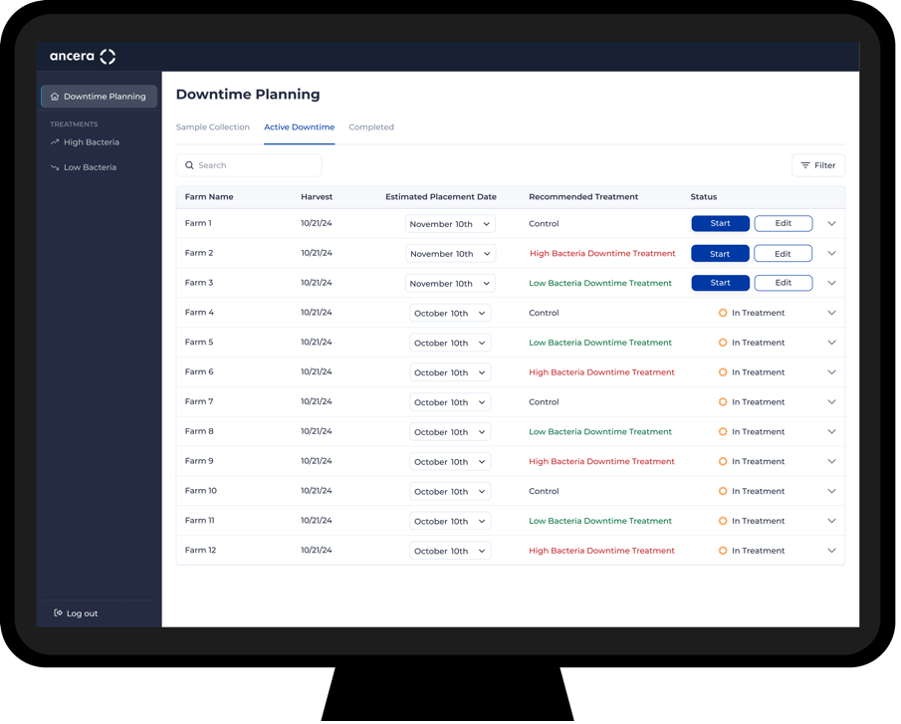
This precision approach is already yielding dramatic results:
Reduced Cost ofTreatment, More Liveweight:
By safely shaving just one day off the average downtime per grow-out, the complex saves $1,500 per farm per grow out in treatment costs. Factoring in the additional pounds sent to the plant, that adds up to $1.48 million in new profits over one year.
Reduced Mortality Rates:
With tailored treatments and optimized conditions, mortality is projected to drop from 7.7% to 4.9%.This improvement nets another $1.44 million in profits.
Improved Feed ConversionRatio (FCR):
Birds are reaching fuller, more consistent weights without incurring additional feed costs, optimizing FCR by two points and adding $1.39 million per year in profits.
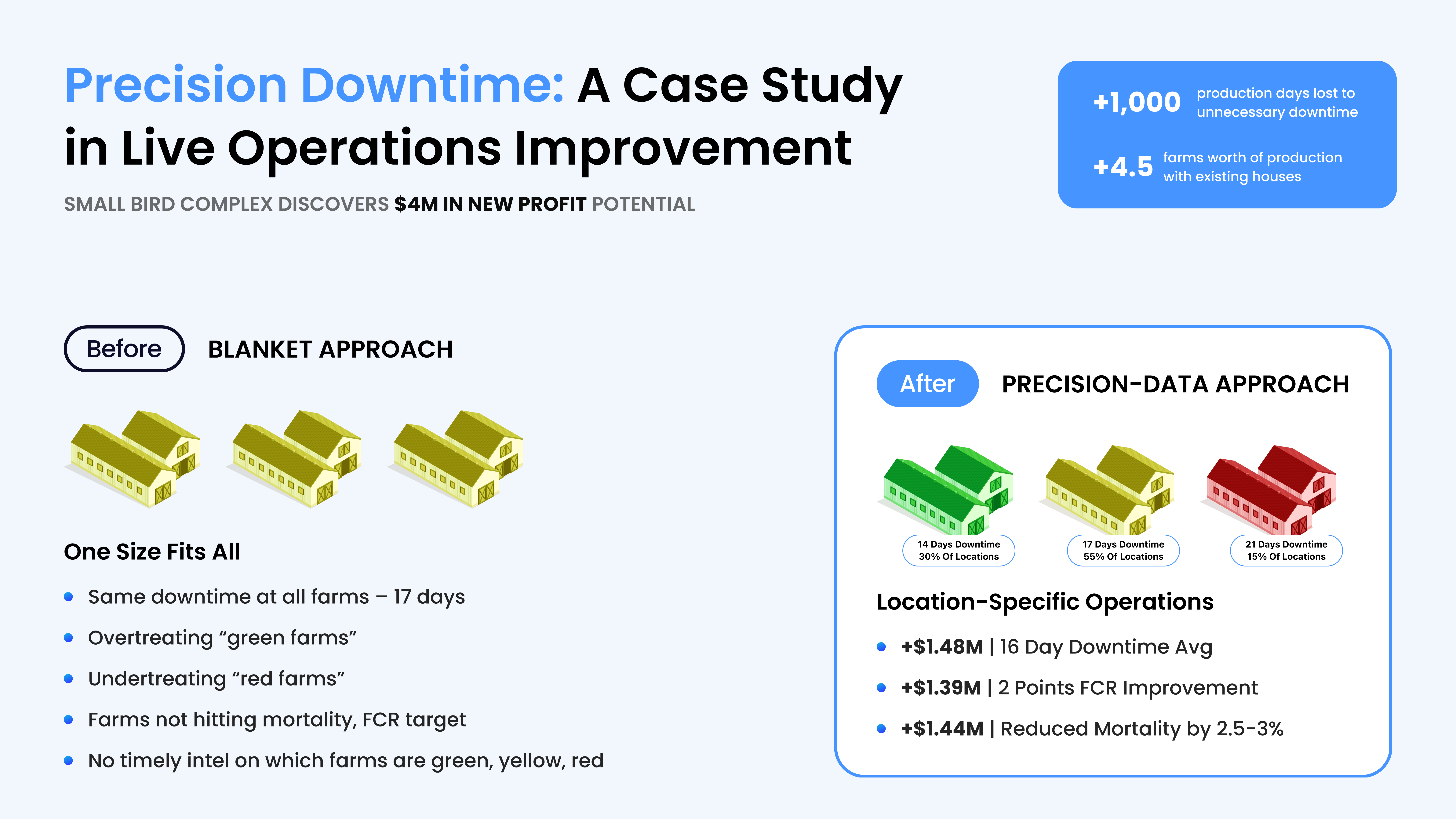
The Cost of Default Thinking vs. the Future of Data-Driven Decisions
Default downtime schedules have persisted because they were convenient given the need for industrial scale live operations with little data. But as this case study shows, they’re also wildly inefficient to the tune of $4.31M. Treating every farm the same way fails to realize their full profit generating potential.
In poultry, each decision is multiplied by a million. The industry can no longer afford the comfort blanket of blanket approaches. Ancera’s Precision Downtime software offers a modern and profitable solution — one that’s grounded in data, tailored to each farm, and laser-focused on financial performance.
You need to win the war of efficiency to stay competitive in a margin intensive industry. To win a war, you need the best possible intelligence.
Request a demo to learn how you can put precision into practice at your complex.